SCADA Systems Components: Programmable Logic Controllers (PLCs) ⚡
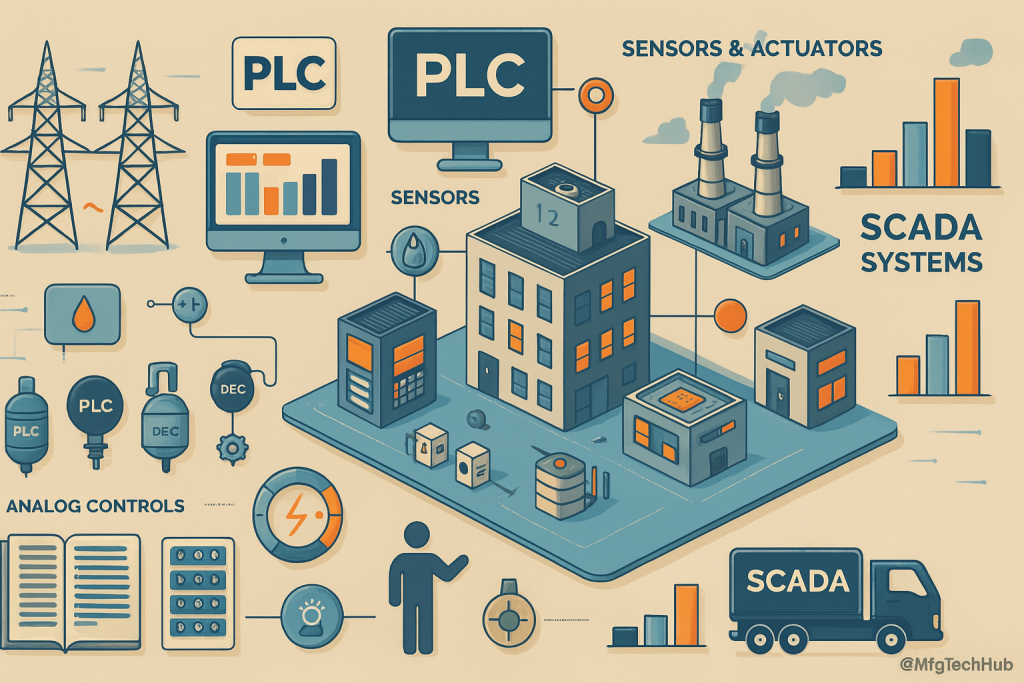
1. What is a PLC in SCADA?
A Programmable Logic Controller (PLC) is a ruggedized industrial computer that plays a crucial role in SCADA systems. It executes real-time control by processing input signals from sensors, switches, and other field devices, then sending commands to actuators and machines.
🔹 Example: In a water treatment plant, a PLC controls pumps and valves based on tank level sensors to maintain optimal water flow.
2. Key Functions of PLCs in SCADA
A. Data Acquisition and Processing
- 📊 Reads signals from field sensors (e.g., temperature, pressure, flow).
- 🔄 Converts analog signals into digital data for SCADA processing.
- 📡 Communicates with SCADA systems via Modbus, Ethernet/IP, OPC UA.
🔹 Example: In an oil refinery, a PLC reads flow rates from pipelines and sends data to SCADA, triggering alarms for pressure anomalies.
B. Logic Execution and Process Control
- 🕹️ Executes control logic based on pre-programmed instructions.
- ⚡ Automates industrial processes, reducing human intervention.
- 🔄 Optimizes efficiency by controlling motors, valves, and actuators.
🔹 Example: In an automotive factory, a PLC controls robotic arms in assembly lines to ensure precise welding and material handling.
C. Alarm and Event Management
- 🚨 Monitors process variables for deviations.
- 📢 Triggers alarms for faults, safety breaches, or system failures.
- 📜 Logs historical events for troubleshooting and compliance.
🔹 Example: A PLC monitors gas pipeline pressure and activates an emergency shut-off valve if levels exceed safety limits.
D. Communication with SCADA Systems
- 🔗 Acts as a bridge between field devices and SCADA software.
- 📡 Uses industrial protocols (Modbus, Profibus, DNP3) for seamless integration.
- 🌍 Supports remote monitoring and control over the network.
🔹 Example: In smart grids, PLCs transmit voltage and load data from substations to SCADA for real-time grid balancing.
3. PLCs vs. RTUs: Key Differences
Feature | Programmable Logic Controller (PLC) | Remote Terminal Unit (RTU) |
---|---|---|
Primary Function | Executes logic and automation | Data acquisition and remote control |
Processing Power | High-speed logic execution | Lower processing speed |
Data Storage | Limited memory for local storage | Stores historical data |
Communication | Uses Ethernet/IP, Modbus, OPC UA | Uses DNP3, IEC 60870 |
Best For | Factory automation, high-speed control | Remote locations, large-scale SCADA networks |
4. Applications of PLCs in SCADA
A. Manufacturing Automation
- 🏭 Controls robotic arms, conveyors, and production lines.
- 📊 Monitors product quality using sensor feedback.
- 💡 Optimizes power usage in high-speed operations.
🔹 Example: A PLC in a bottling plant synchronizes conveyors to fill, cap, and label bottles accurately.
B. Energy and Utilities
- ⚡ Monitors and controls power grids, substations, and turbines.
- 🔍 Optimizes energy distribution based on real-time demand.
- 🛡️ Ensures grid stability with load balancing automation.
🔹 Example: A PLC in a wind farm adjusts turbine blades to maximize power generation based on wind speed.
C. Oil and Gas Industry
- 🛢️ Regulates pipeline flow, pressure, and storage tanks.
- ⛽ Automates drilling operations for safety and efficiency.
- 🚨 Triggers emergency shutdowns in case of system failure.
🔹 Example: A PLC at an offshore rig controls drilling equipment while continuously monitoring pressure levels to prevent blowouts.
D. Water and Wastewater Management
- 💦 Monitors tank levels, pump operations, and chemical dosing.
- 🔄 Optimizes water distribution by adjusting pump speeds.
- 🚨 Detects leaks or contamination and triggers alarms.
🔹 Example: A PLC in a wastewater treatment plant adjusts aeration levels based on oxygen sensor data to maintain water quality.
5. Modern Trends in PLC Technology
- 🚀 Edge Computing with PLCs – Process data locally before sending it to SCADA.
- 📡 Cloud-Connected PLCs – Remote access and real-time analytics via cloud platforms.
- 🛡️ Cybersecurity Integration – Enhanced firewall protection for PLC networks.
- 🤖 AI and Machine Learning – Predictive maintenance and fault detection automation.
- 📱 Mobile-Based Monitoring – PLCs support smartphone integration for mobile control.
🔹 Example: In smart manufacturing, AI-enabled PLCs analyze production data in real-time, predict failures, and recommend process improvements.
Programmable Logic Controllers (PLCs) are the brain of industrial automation, ensuring real-time control, process optimization, and seamless integration with SCADA systems. With advancements in IoT, cloud computing, and AI, PLCs are becoming smarter, faster, and more secure, playing a critical role in Industry 4.0 and smart automation.