Introduction to PLCs
What is a Programmable Logic Controller (PLC)?
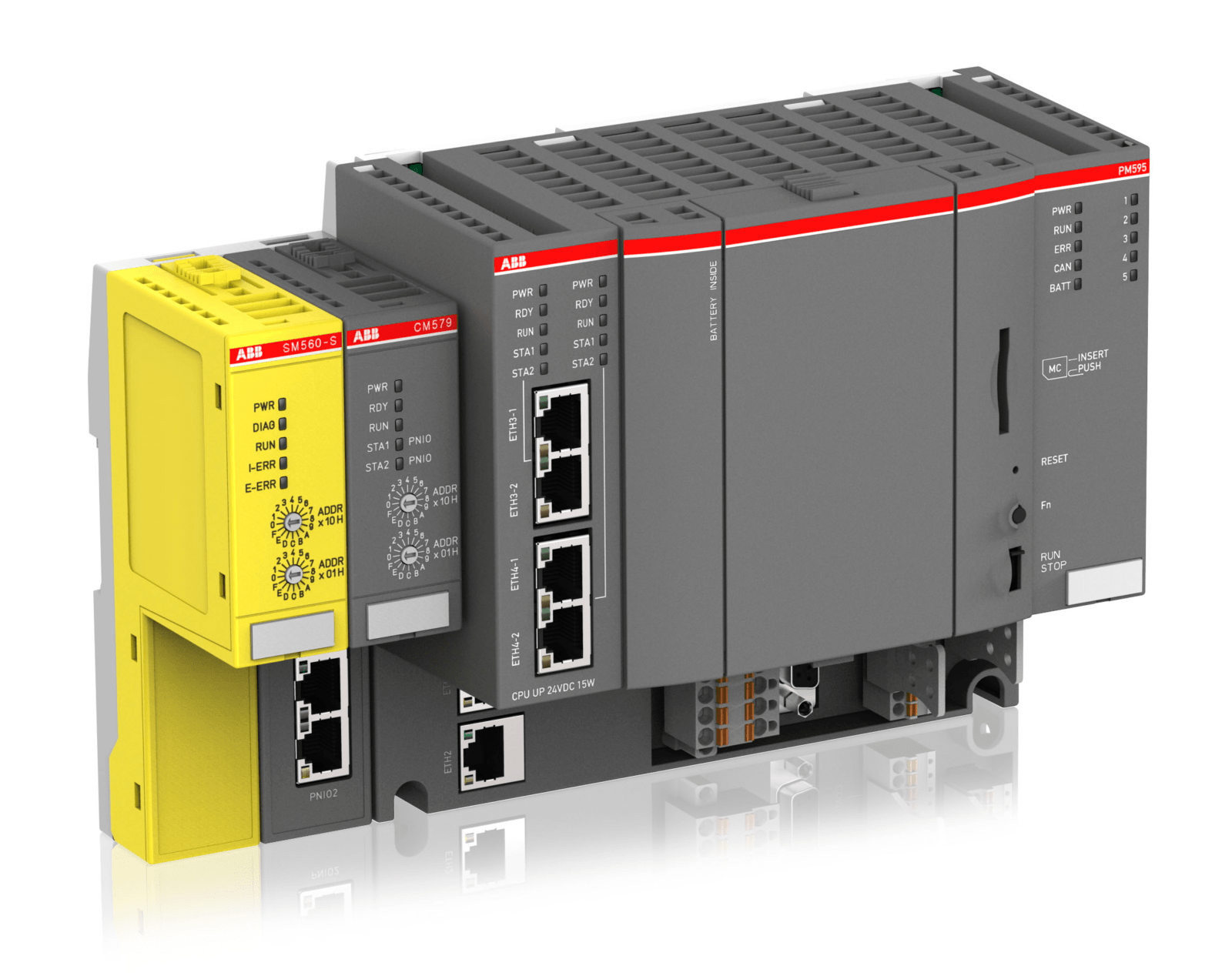
In today's rapidly advancing world of industrial automation, Programmable Logic Controllers (PLCs) play a crucial role in controlling machinery and processes across various industries. From manufacturing plants to power grids, PLCs ensure that machines operate efficiently, safely, and reliably.
A PLC is an industrial computer designed to automate mechanical and electrical processes, such as operating conveyor belts, robotic arms, packaging systems, and even large-scale industrial machinery. Unlike traditional computers, PLCs are built to withstand harsh environments, including extreme temperatures, vibrations, and electrical noise.
Why are PLCs Important?
PLCs replace traditional relay-based control systems, making automation more efficient, cost-effective, and adaptable. They provide:
- ✔ Faster execution of control tasks
- ✔ Real-time monitoring and data collection
- ✔ Flexibility for modifications and upgrades
- ✔ Improved reliability and reduced downtime
Industries like manufacturing, energy, pharmaceuticals, automotive, and smart cities rely on PLCs for automating complex processes.
How Do PLCs Work?
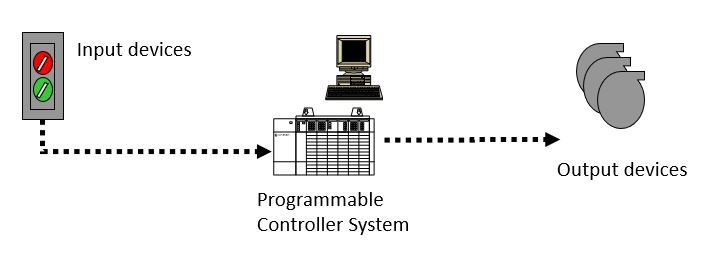
PLCs function as the brain of an automated system. They process inputs, execute programmed logic, and generate outputs to control devices like motors, valves, and sensors. The basic working of a PLC follows this three-step cycle:
- Input Scan – The PLC reads data from sensors, switches, or other input devices.
- Program Execution – It processes the logic based on pre-written instructions.
- Output Control – The PLC sends signals to activate or deactivate actuators, motors, and other machinery.
This cycle repeats continuously in milliseconds, ensuring real-time operation and control.
Key Features of PLCs
PLCs stand out due to their robust design and advanced functionalities. Some key features include:
- ✅ Modular & Scalable Design – Easily expandable with additional modules (I/O, communication, etc.).
- ✅ Real-Time Processing – Executes commands within milliseconds, ensuring precision.
- ✅ Rugged & Durable – Designed to function in extreme industrial environments.
- ✅ Network Communication – Supports Ethernet, Modbus, Profibus, and other industrial protocols.
- ✅ High Reliability – Less prone to failures compared to traditional relay systems.
- ✅ Easy Programming & Troubleshooting – Uses graphical interfaces like Ladder Logic (LD) and Function Block Diagram (FBD).
Types of PLCs
PLCs come in different sizes and configurations, depending on industry requirements. The two main types are:
1. Compact PLCs
- All-in-one unit with limited input/output (I/O) options.
- Ideal for small-scale applications like packaging systems, elevators, and HVAC automation.
2. Modular PLCs
- Designed for large industrial automation needs.
- Offers flexibility to expand I/O modules, suitable for complex manufacturing plants, power stations, and process industries.
Choosing the right PLC depends on system complexity, scalability needs, and communication requirements.
Real-World Applications of PLCs
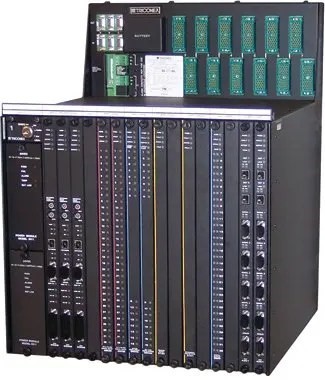
PLCs are widely used in various industries, including:
- 🏭 Manufacturing – Automating assembly lines, robotic welding, and quality inspection.
- 🚆 Transportation – Controlling railway signaling systems, airport baggage handling, and traffic lights.
- ⚡ Energy Sector – Managing power grids, wind turbines, and hydroelectric plants.
- 🌊 Water Treatment – Regulating pumps, chemical dosing, and filtration processes.
- 🏢 Building Automation – Optimizing HVAC, lighting, and security systems in smart buildings.
The versatility and reliability of PLCs make them indispensable in modern industrial automation.
Advantages of Using PLCs
PLCs have revolutionized industrial automation by offering several advantages over traditional control systems:
1. Increased Efficiency
PLCs operate at high speed, minimizing errors and downtime while boosting production efficiency.
2. Easy Troubleshooting & Maintenance
PLC programs provide real-time diagnostics and fault detection, making it easier to identify and resolve issues.
3. Cost-Effectiveness
Although initial installation can be expensive, PLCs reduce long-term maintenance costs by improving reliability and efficiency.
4. Flexibility & Scalability
Unlike hardwired relay systems, PLCs can be reprogrammed and expanded to accommodate changing production demands.
5. Integration with Smart Technologies
Modern PLCs support IoT, cloud computing, and Industry 4.0, enabling remote monitoring and predictive maintenance.
PLCs are the foundation of industrial automation, offering speed, reliability, and flexibility for various industries. Whether in manufacturing, power generation, transportation, or smart infrastructure, PLCs continue to transform operations through real-time control and intelligent automation.
Understanding how PLCs work, their features, and advantages is crucial for anyone involved in automation, electrical engineering, or industrial operations. As technology advances, PLCs will continue to evolve, integrating with AI, IoT, and cloud computing, paving the way for smarter and more efficient industrial processes.