MES Technology Future Trends: Integration with Industry 4.0
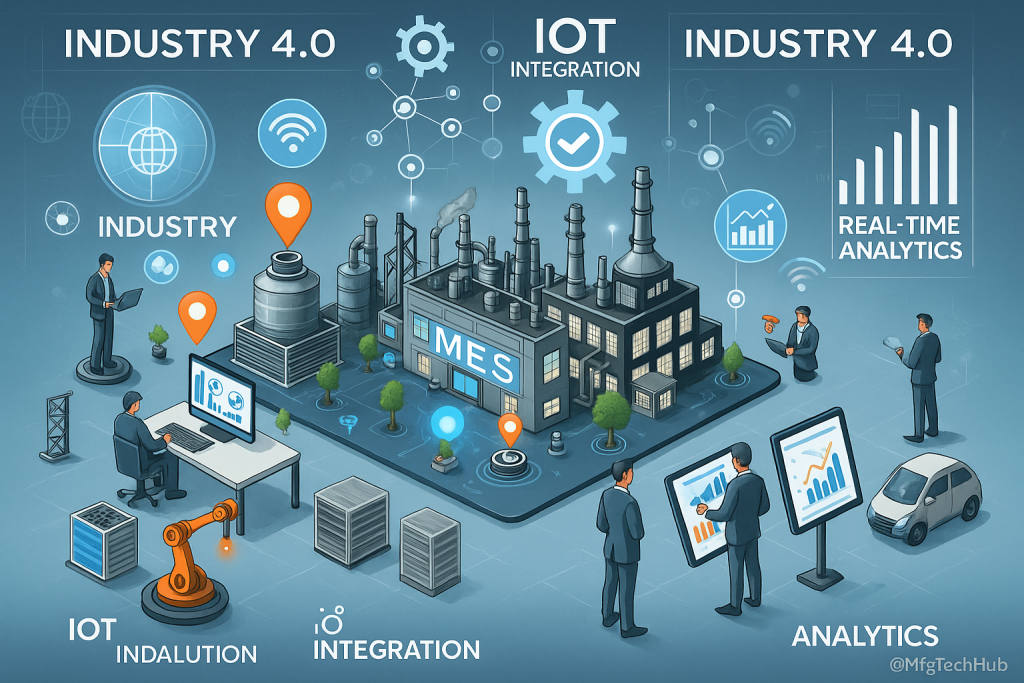
The Fourth Industrial Revolution, also known as Industry 4.0, is transforming the way factories operate. Unlike earlier industrial revolutions that introduced steam power, electricity, and computing, Industry 4.0 is about intelligent connectivity. It leverages the Internet of Things (IoT), Artificial Intelligence (AI), Big Data analytics, and cloud computing to create factories that are more responsive, flexible, and efficient.
At the center of this transformation lies the Manufacturing Execution System (MES). Traditionally, MES served as a system for tracking production, monitoring performance, and ensuring compliance. But in the context of Industry 4.0, MES evolves into a digital backbone — a platform that connects machines, workers, and business systems, providing real-time visibility and enabling predictive decision-making. By integrating MES with Industry 4.0 technologies, manufacturers can reduce downtime, improve quality, and unlock levels of agility never before possible.
Key Features of MES Integration with Industry 4.0
1. IoT-Enabled Manufacturing
IoT is the foundation of Industry 4.0. By connecting sensors and devices across machines, MES gains access to real-time data streams. This allows factories to move from reactive approaches to proactive and predictive strategies.
- Example: Automotive Industry — An automotive plant integrates IoT sensors into robotic welding stations. If a robot arm starts vibrating beyond safe limits, the IoT-enabled MES detects the anomaly and schedules predictive maintenance before it causes downtime.
2. AI-Powered Analytics
Factories generate vast amounts of data every day, but raw data is not useful unless analyzed intelligently. AI-powered MES can process this data to identify patterns, forecast demand, and prescribe actions.
- Example: Food Processing — A packaged food manufacturer uses AI-driven MES to forecast seasonal demand. Instead of overproducing or underproducing, the system balances production schedules with real-time sales data, reducing waste and increasing profitability.
3. Digital Twin Technology
A digital twin is a virtual replica of a factory or production line. By feeding MES data into the twin, manufacturers can simulate scenarios, optimize layouts, and test new strategies without halting production.
- Example: Electronics Manufacturing — Before launching a new smartphone model, an electronics company creates a digital twin of its assembly line. By testing MES-driven configurations virtually, they minimize risks and optimize throughput before changes go live on the shop floor.
4. Autonomous Machines and Robotics
Modern MES is no longer limited to human-machine interaction. It increasingly coordinates with autonomous guided vehicles (AGVs), robotic arms, and even drones, orchestrating tasks across the factory floor with precision.
- Example: Pharmaceutical Industry — In a sterile manufacturing plant, MES directs AGVs to transport raw materials. This reduces human contact, minimizes contamination risks, and ensures compliance with strict pharmaceutical regulations.
5. Real-Time Data and Cloud Connectivity
Cloud computing allows MES to extend beyond the factory floor. With cloud-based MES, manufacturers can oversee operations across multiple global sites in real-time. Cloud also ensures scalability, disaster recovery, and remote access.
- Example: Aerospace Manufacturing — A global aerospace company uses cloud-enabled MES to coordinate production across sites in different countries. Quality data, machine performance, and inventory levels are updated instantly, ensuring all facilities operate to the same standard.
Benefits of MES Integration with Industry 4.0
Feature | Benefit |
---|---|
IoT-Enabled Manufacturing | Predictive maintenance reduces downtime and improves machine life. |
AI-Powered Analytics | Optimized scheduling and forecasting boost efficiency and reduce waste. |
Digital Twin Technology | Simulations reduce risks and allow smarter planning of new processes. |
Autonomous Machines | Automation reduces errors, speeds up processes, and enhances safety. |
Cloud Connectivity | Real-time data supports global collaboration and disaster recovery. |
Steps to Integrate MES with Industry 4.0
- Upgrade Infrastructure — Invest in IoT-enabled sensors, secure networks, and scalable cloud platforms to ensure MES integration is reliable.
- Implement Interoperability Standards — Adopt open protocols such as OPC UA and MQTT to enable smooth communication between MES, machines, and ERP systems.
- Adopt AI and Machine Learning — Integrate AI tools into MES for predictive insights, anomaly detection, and smarter scheduling.
- Train Employees — Train operators, managers, and engineers on data-driven decision-making and collaborative human-robot workflows.
- Monitor and Optimize — Continuously refine processes using KPIs, data feedback loops, and pilot projects to stay aligned with evolving technologies.
Future Possibilities
- Smart Supply Chains — MES will link suppliers, logistics, and customers for real-time visibility and automated replenishment.
- Augmented Reality (AR) — AR headsets connected with MES will provide technicians with step-by-step repair and maintenance guidance.
- Blockchain Integration — Blockchain will secure MES data, ensuring tamper-proof traceability of products from raw material to final delivery.
- Edge Computing — By combining MES with edge devices, manufacturers will process data locally for faster decision-making without relying solely on the cloud.
Conclusion
The integration of MES with Industry 4.0 is not just an upgrade — it is a revolution in how manufacturing is managed. By combining IoT, AI, robotics, digital twins, and cloud systems, MES becomes the intelligent control hub of smart factories. This integration ensures greater efficiency, improved product quality, enhanced flexibility, and global competitiveness.
Manufacturers that embrace MES-Industry 4.0 integration today will be better positioned for the future. They will not only achieve operational excellence but also adapt dynamically to market changes, withstand disruptions, and unlock new opportunities for innovation in the global industrial landscape.