MES (Manufacturing Execution System) Introduction
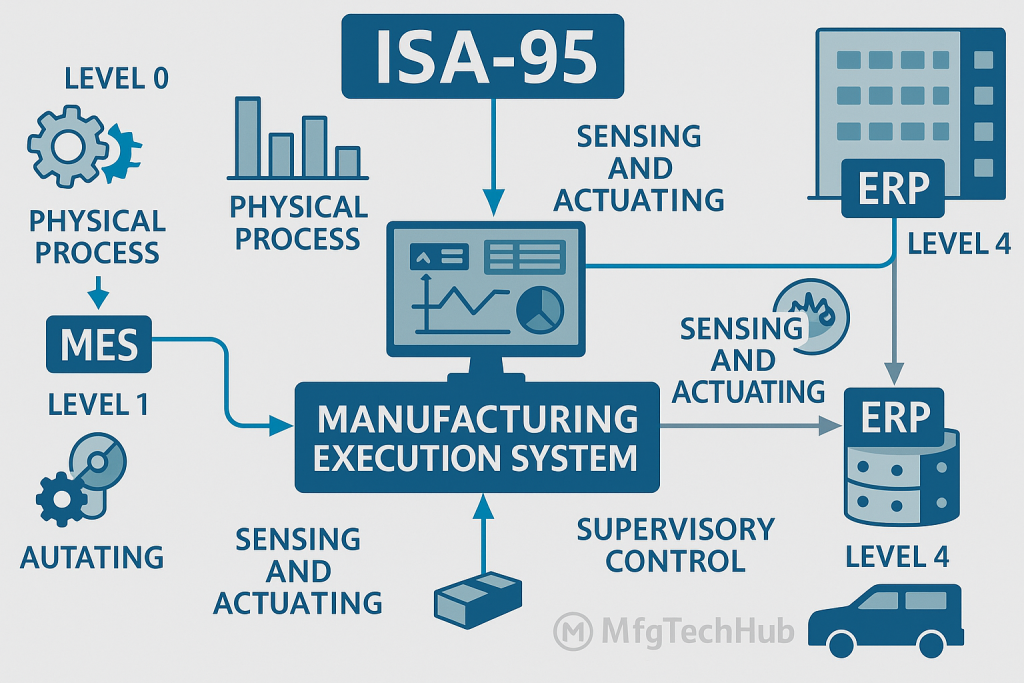
In today’s fast-evolving manufacturing world, optimizing production processes while maintaining high-quality standards is critical for success. This is where the Manufacturing Execution System (MES) plays a role. MES serves as the bridge between planning systems like ERP (Enterprise Resource Planning) and the physical shop floor, providing real-time data and control to streamline manufacturing operations.
What is MES?
Definition by ISA
The International Society of Automation (ISA) defines MES as a system that connects, monitors, and controls complex manufacturing systems and data flows on the factory floor. It provides a comprehensive understanding of the “who, what, when, where, why, and how” of manufacturing operations.
Definition by MESA
The Manufacturing Enterprise Solutions Association (MESA) defines MES as a dynamic information system that drives the effective execution of manufacturing operations by managing and delivering data in real-time.
Key Functions of MES
MES offers the following core functionalities:
- Scheduling: Optimizes resource allocation for machines, labor, and materials.
- Tracking and Traceability: Records every step of the manufacturing process for regulatory compliance and quality assurance.
- Data Collection and Analysis: Provides real-time insights into machine performance, production rates, and quality.
- Quality Management: Ensures consistent product quality with in-process checks.
- Work Order Management: Tracks progress, timelines, and resource utilization.
What is MOM (Manufacturing Operations Management)?
MOM is a broader concept encompassing MES and other manufacturing systems. While MES focuses specifically on execution and operations on the shop floor, MOM includes:
- Production Management: Planning and monitoring production schedules.
- Quality Management: Ensuring products meet predefined quality standards.
- Inventory Management: Tracking raw materials and finished goods.
- Maintenance Management: Scheduling and optimizing equipment maintenance to minimize downtime.
In short, MES is a subset of MOM, focusing primarily on real-time execution and visibility of manufacturing processes.
Understanding the ISA-95 Model
The ISA-95 model, developed by the International Society of Automation, is a standard for integrating enterprise and control systems. It serves as a framework to define interfaces, workflows, and responsibilities between different layers of a manufacturing organization.
Key Levels of ISA-95
ISA-95 divides a manufacturing system into five hierarchical levels:
Level | Name | Description |
---|---|---|
Level 0 | Physical Process | The actual production processes, including machinery and equipment. |
Level 1 | Sensing and Actuating | Control devices such as PLCs, sensors, and actuators that monitor and execute physical processes. |
Level 2 | Supervisory Control | Systems like SCADA and DCS that monitor, control, and collect data from Level 1 systems. |
Level 3 | MES (Manufacturing Execution System) | Real-time management of production processes, tracking, and traceability. |
Level 4 | ERP (Enterprise Resource Planning) | Enterprise-level systems for planning, finance, supply chain management, and overall resource allocation. |
MES in the ISA-95 Framework
- Connecting ERP and Shop Floor: MES operates at Level 3, acting as a translator between the strategic goals of ERP (Level 4) and the real-time data from the shop floor (Levels 0-2).
- Real-Time Control: MES ensures that production processes align with enterprise goals, enabling adjustments in schedules, resource utilization, and quality checks.
- Data Aggregation: It consolidates shop floor data for analysis at higher levels (e.g., ERP for planning and reporting).
Benefits of MES within ISA-95
Feature | Impact |
---|---|
Data Transparency | Provides real-time visibility into shop floor operations. |
Standardization | Aligns manufacturing processes across plants with enterprise-wide goals. |
Integration with ERP | Seamlessly connects operational data from the shop floor to enterprise planning systems. |
Regulatory Compliance | Facilitates compliance by maintaining detailed production records and traceability. |
Increased Efficiency | Reduces waste and downtime by identifying and resolving bottlenecks in real-time. |
MES vs MOM: Key Differences
While MES focuses primarily on production execution, MOM has a broader scope, encompassing all aspects of manufacturing operations.
Aspect | MES (Manufacturing Execution System) | MOM (Manufacturing Operations Management) |
---|---|---|
Focus | Real-time execution of manufacturing processes. | End-to-end management of manufacturing operations. |
Scope | Limited to shop floor management. | Includes production, quality, maintenance, and inventory. |
Role | Provides real-time visibility and control. | Ensures alignment between production, business goals, and quality. |
Real-World Example of MES in Action
Imagine an electronics manufacturing plant producing smartphones:
- ERP (Level 4): Plans daily production targets, resources, and schedules.
- MES (Level 3): Tracks production in real time, ensuring assembly lines meet quality and efficiency standards. It detects deviations and adjusts workflows dynamically.
- SCADA (Level 2): Supervises machine performance, sending data to MES for analysis.
- PLC (Level 1): Executes precise control of robotic arms assembling components.
The MES ensures that any production issue—such as a defective component—is flagged immediately, preventing further wastage and maintaining product quality.
Benefits of MES
Benefit | Description |
---|---|
Improved Productivity | Optimizes the use of machines, labor, and materials for maximum efficiency. |
Enhanced Quality Control | Real-time quality checks ensure consistent product standards. |
Traceability | Tracks every step of the production process, ensuring regulatory compliance and ease of recall management. |
Real-Time Decision-Making | Provides actionable insights to respond swiftly to issues on the shop floor. |
Cost Savings | Reduces wastage, downtime, and inefficiencies, resulting in cost reductions. |