MES History and Evolution
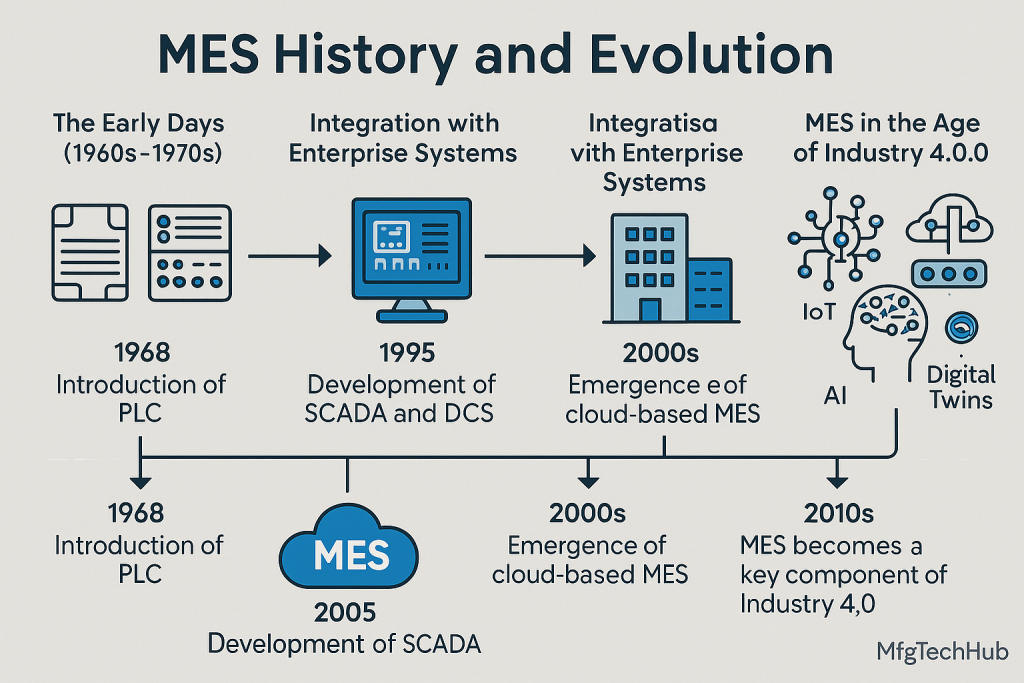
The Manufacturing Execution System (MES) has a rich history that mirrors the evolution of industrial processes and automation. From its beginnings in basic production monitoring to the highly integrated and intelligent systems of today, MES has played a transformative role in manufacturing. Each decade introduced breakthroughs that changed how factories operated, improved decision-making, and laid the groundwork for today’s smart factories.
The Early Days: Origins of MES (1960s - 1970s)
In the 1960s and 1970s, factories were heavily dependent on manual operations and paper-based records. While these methods worked, they were slow, error-prone, and limited in scope. Data was often delayed, meaning managers could not make real-time decisions. At this stage:
- Control Systems: The introduction of programmable logic controllers (PLCs) in the late 1960s marked a shift from hardwired relay systems to programmable devices, offering greater flexibility.
- Challenges: Manufacturers faced inefficiencies, inconsistent product quality, and a lack of real-time process visibility.
This period laid the foundation for MES by highlighting the critical need for better control and coordination across operations. Factories recognized that as products became more complex, manual methods were not sustainable.
The Rise of Automation: MES in the 1980s
The 1980s introduced a wave of automation technologies that revolutionized manufacturing processes. Key developments included:
- Introduction of SCADA and DCS:
- SCADA (Supervisory Control and Data Acquisition) and DCS (Distributed Control Systems) enabled real-time monitoring and control of production lines.
- Operators could now track performance on screens, reducing reliance on manual observations.
- These systems paved the way for MES by capturing real-time production data, a cornerstone of modern manufacturing intelligence.
- Emergence of Early MES Systems:
- Software applications started to appear for managing tasks like production scheduling, labor tracking, and material usage.
- These systems were limited in scope and usually standalone, but they showed the potential of digital shop floor management.
By the end of the 1980s, industries such as automotive and aerospace began experimenting with early MES solutions to improve efficiency in increasingly complex supply chains.
Integration with Enterprise Systems: MES in the 1990s
The 1990s marked a turning point when MES moved beyond standalone applications and became a critical layer in manufacturing IT architecture. This was the decade when integration became the focus:
- Advent of ERP Systems:
- Enterprise Resource Planning (ERP) systems such as SAP and Oracle became widely adopted, enabling centralized management of finance, HR, and supply chain.
- However, ERP lacked the real-time responsiveness needed for shop floor activities.
- MES Bridges the Gap:
- MES emerged as the bridge between ERP and shop floor systems like PLCs, SCADA, and DCS.
- It provided real-time production tracking, quality assurance, and traceability.
- Standardization Begins:
- The ISA-95 standard was introduced, defining clear roles for MES in the manufacturing pyramid. This made implementations more consistent across industries.
During this era, industries like pharmaceuticals and food manufacturing adopted MES to meet growing regulatory requirements for traceability and quality control.
The Era of Digital Transformation: MES in the 2000s
The 2000s brought widespread digitalization, enabling MES to become smarter and more scalable. Several advances shaped this phase:
- Internet Connectivity:
- Industrial Ethernet replaced older communication protocols, making data exchange faster and more reliable.
- MES could now connect seamlessly with machines, enterprise systems, and even remote facilities.
- Cloud-Based MES:
- Cloud adoption allowed MES vendors to offer scalable, subscription-based solutions.
- Smaller manufacturers who could not afford large IT infrastructures benefited from cloud MES platforms.
- Advanced Analytics:
- Real-time dashboards, key performance indicators (KPIs), and predictive analytics became standard features.
- MES transitioned from being a reporting tool to a decision-support system.
This was also the decade when global manufacturing networks expanded. MES helped companies manage multiple plants across different geographies while maintaining consistency in quality and compliance.
MES in the Age of Industry 4.0 (2010s and Beyond)
The 2010s ushered in Industry 4.0, redefining how MES operates. Today, MES is no longer just about tracking production; it is an intelligent hub that connects every element of the factory:
- IoT Integration: Sensors, RFID tags, and connected devices feed real-time data directly into MES, giving manufacturers complete visibility over machines and processes.
- AI and Machine Learning: MES systems use AI to predict failures, optimize scheduling, and even recommend process improvements autonomously.
- Digital Twins: Factories can simulate processes using digital replicas, allowing MES to test scenarios before implementing them on the shop floor.
- Mobile Access: Plant managers can monitor and control operations through mobile apps, ensuring flexibility and faster response times.
In sectors such as electronics, aerospace, and pharmaceuticals, MES has become indispensable for managing complex, high-precision processes.
Key Milestones in MES Evolution
Some of the major milestones that shaped MES include:
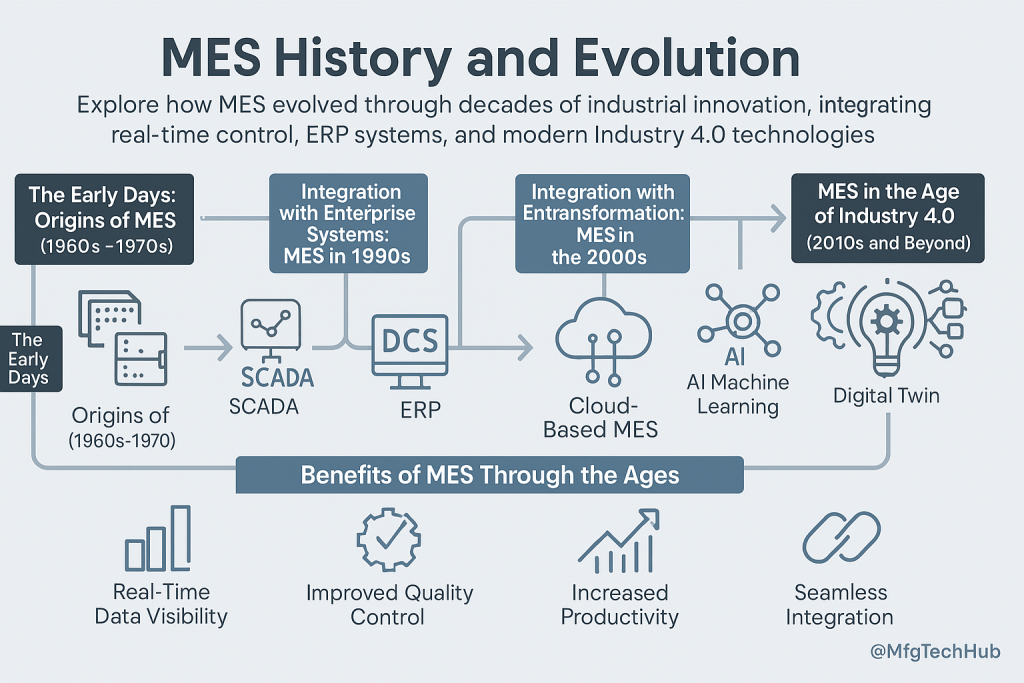
Year | Milestone |
---|---|
1968 | Introduction of the first PLC by Modicon, revolutionizing process control. |
1980s | Development of SCADA and DCS for real-time process supervision. |
1995 | Release of ISA-95, defining MES standards and integration roles. |
2000s | Adoption of cloud MES solutions and advanced analytics tools. |
2010s | MES integrates IoT, AI, digital twins, and mobility as part of Industry 4.0. |
Benefits of MES Through the Ages
As MES evolved, it consistently delivered value to manufacturers by addressing their most pressing needs:
- Real-Time Data Visibility: Transitioning from delayed manual logs to real-time dashboards transformed decision-making.
- Improved Quality Control: Each generation of MES introduced better methods to monitor quality during production, reducing defects and recalls.
- Increased Productivity: Automation, analytics, and AI-driven insights have helped factories maximize throughput and minimize downtime.
- Seamless Integration: From standalone systems to interconnected networks, MES has bridged enterprise planning with shop floor execution.
- Regulatory Compliance: Particularly in industries like pharmaceuticals and food, MES ensures adherence to strict standards with full traceability.
The Future of MES
Looking ahead, MES will continue to evolve alongside technologies such as 5G, blockchain, and edge computing. Future MES platforms will focus even more on cybersecurity, sustainability, and autonomous decision-making. By combining data from across the supply chain, MES will evolve into a central intelligence layer for the factory of the future, driving not just operational efficiency but also environmental responsibility and customer satisfaction.
In short, the history of MES is a story of continuous innovation. From its humble beginnings in the age of relay logic to today’s AI-powered platforms, MES has been the backbone of industrial progress. As Industry 4.0 and beyond unfold, MES will remain a critical enabler of smart, connected, and resilient manufacturing.